Comprehensive Insights into Industrial Vacuum System Design
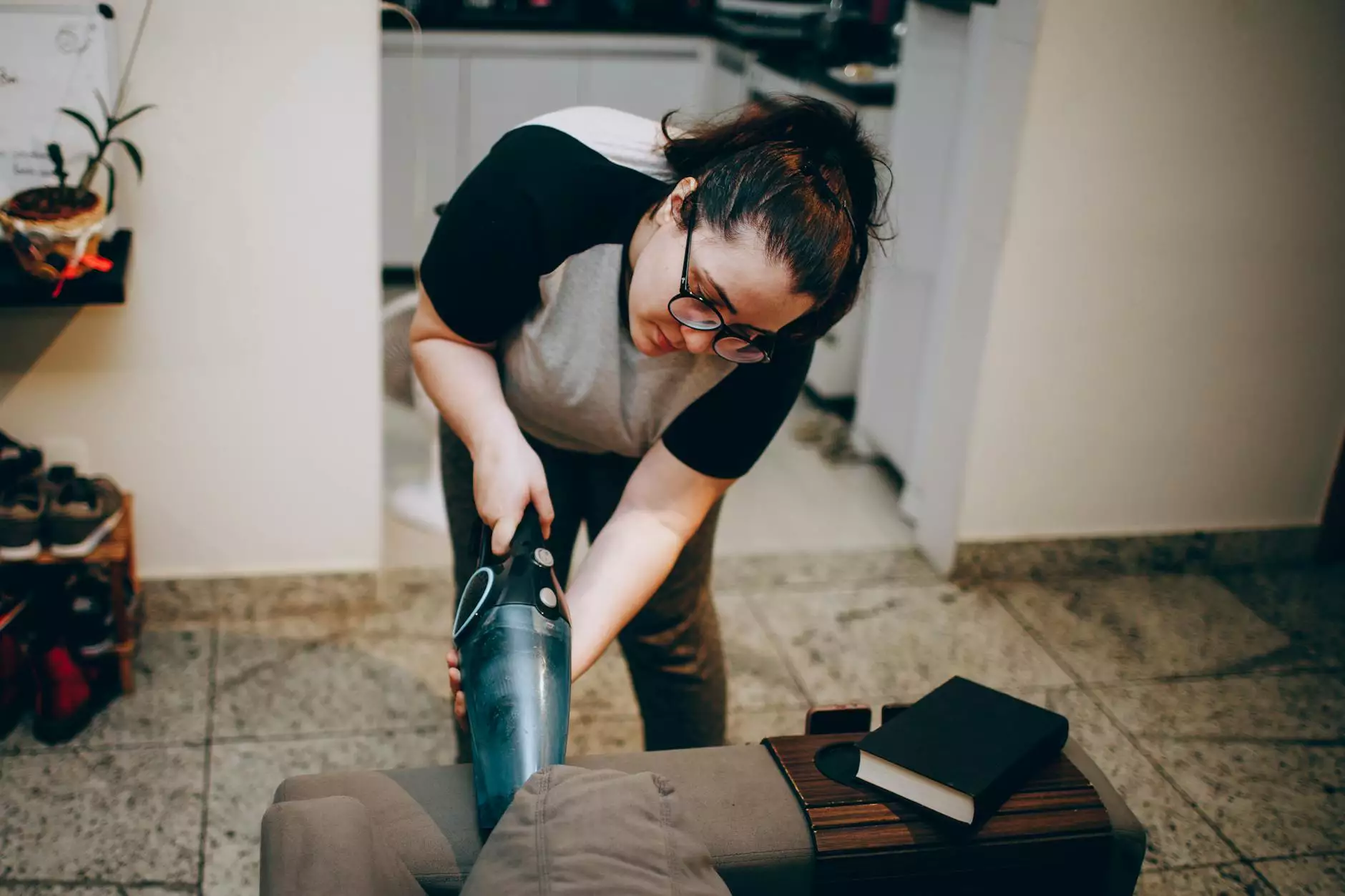
The modern industrial landscape is constantly evolving, challenging businesses to optimize their operations. One crucial aspect that many industries overlook is the design of industrial vacuum systems. These systems not only enhance efficiency but also ensure a cleaner, safer work environment. Whether you’re in manufacturing, food processing, or any sector where dust and debris management is critical, understanding the fundamentals of industrial vacuum system design is essential.
Understanding Industrial Vacuum Systems
At its core, an industrial vacuum system is a complex network of components designed to remove particulates, liquids, and other contaminants from the air and surfaces within an industrial setting. A well-designed system will consist of several key components that work together seamlessly.
Key Components of an Industrial Vacuum System
- Vacuum Pumps: These are the heart of any vacuum system. They create the suction necessary to move air and contaminants through the system.
- Filtration Units: Essential for trapping particulates and preventing them from re-entering the environment. These may include HEPA filters, bag filters, and cyclone separators.
- Hoses and Nozzles: Customized hoses and nozzles are imperative for effective waste collection, allowing for flexibility and ease of use across various industrial applications.
- Control Systems: Modern vacuum systems employ advanced control systems for monitoring and automation, allowing for a more efficient operation.
- Tanks and Collection Systems: These components store the collected debris, ensuring that waste is managed efficiently.
Benefits of Effective Industrial Vacuum System Design
Investing in an optimized industrial vacuum system design offers numerous advantages that impact both productivity and cleanliness in an industrial setting. Below are some of the notable benefits:
1. Enhanced Safety Standards
By effectively removing dust and debris, industrial vacuum systems promote a safer work environment. Less airborne contamination means reduced health risks for employees, leading to fewer accidents and a decrease in work-related illnesses.
2. Improved Product Quality
In manufacturing processes, contaminants can adversely affect product quality. An efficient vacuum system minimizes the risk of defects, ensuring that the products meet the highest standards.
3. Cost Reduction
While there may be an initial investment for high-quality vacuum systems, the long-term cost savings are significant. These systems can lead to lower maintenance costs for machinery, reduced labor costs due to increased efficiency, and fewer product losses due to contamination.
4. Compliance with Regulations
Many industries are subject to strict environmental regulations regarding air quality. A well-designed industrial vacuum system helps ensure compliance with these laws, avoiding potential fines and reputational damage.
Designing an Optimal Industrial Vacuum System
The design process of an industrial vacuum system requires careful consideration of several factors. Here’s a detailed guide on how to approach this crucial task:
1. Assess Your Needs
Start by evaluating your facility and the specific requirements based on the processes carried out. Consider factors such as:
- The type of materials to be collected (dust, liquids, solids)
- The volume of materials generated
- The physical layout of your facility
- Potential environmental and safety regulations
2. Choose the Right Vacuum Type
There are various types of industrial vacuum systems, including:
- Centralized Vacuum Systems: Suitable for large facilities requiring continuous operation, offering high efficiency.
- Portable Vacuum Systems: Ideal for smaller tasks or temporary use, providing flexibility and ease of transport.
- Exhaust Air Filters: Used to purify air emissions from the vacuum process.
3. Component Selection
Each component of the vacuum system must be selected based on performance requirements and compatibility. Considerations include:
- Choosing appropriate vacuum pumps based on the required suction power and application.
- Selecting filtration systems that meet or exceed industry standards for air purity.
- Determining the correct diameter and length of hoses to minimize resistance and maximize airflow.
4. Plan for Maintenance
An effective maintenance strategy is crucial for the longevity of your vacuum system. Implement a routine maintenance schedule that includes:
- Regular checks on pump functionality
- Filter replacements as per manufacturer recommendations
- Inspection of hoses for wear and blockage
Applications of Industrial Vacuum Systems
Industrial vacuum systems are versatile and find applications across various sectors, including:
1. Manufacturing
In manufacturing environments, effective dust control is essential. Vacuum systems help in the collection of metal shavings, wood chips, and other byproducts to enhance workplace safety and streamline production processes.
2. Food Processing
In food processing plants, maintaining a clean environment is non-negotiable. Industrial vacuums ensure the efficient removal of spills and debris, thereby upholding hygiene standards and preventing contamination.
3. Pharmaceuticals
In the pharmaceutical industry, controlling airborne particles is paramount. Vacuum systems are designed to capture fine powders and granules, preventing contamination and ensuring product purity.
4. Construction
Excavation and construction sites generate considerable debris. Industrial vacuum systems effectively mitigate dust and particulate matter, contributing to a safer working environment.
Future Trends in Industrial Vacuum Systems
As industries continue to innovate, several emerging trends are influencing the design and implementation of industrial vacuum systems:
1. Automation and Smart Technologies
The integration of IoT and smart technologies is allowing for more automated and efficient vacuum systems. Real-time monitoring of system performance can predict when maintenance is needed, reducing downtime.
2. Sustainability Focus
With growing environmental concerns, industries are looking for more sustainable vacuum solutions. This includes systems that use less energy and produce fewer emissions.
3. Advanced Filtration Technologies
Recent advancements in filtration technology, including nanofilters and electrostatic filters, are resultant in improved air quality and compliance with stricter regulations.
4. Customization
Tailored solutions are on the rise, with manufacturers offering customized systems that meet specific industrial requirements, ensuring maximum efficiency and effectiveness.
Conclusion
In conclusion, industrial vacuum system design is a vital component in various industries that contributes significantly to operational efficiency and safety. By understanding the components, benefits, and trends affecting vacuum systems, businesses can make informed decisions that enhance their productivity and compliance. From the initial design phase to ongoing maintenance and future innovations, the potential for optimized air quality management and waste reduction is both significant and attainable.
For businesses looking to implement or upgrade their vacuum systems, it is crucial to partner with experienced professionals who can provide tailored solutions based on specific needs. By investing in high-quality industrial vacuum systems, companies can ensure a cleaner workspace, improved product quality, and better overall performance.