Understanding Pump Cavitation: Impacts and Solutions for Your Business
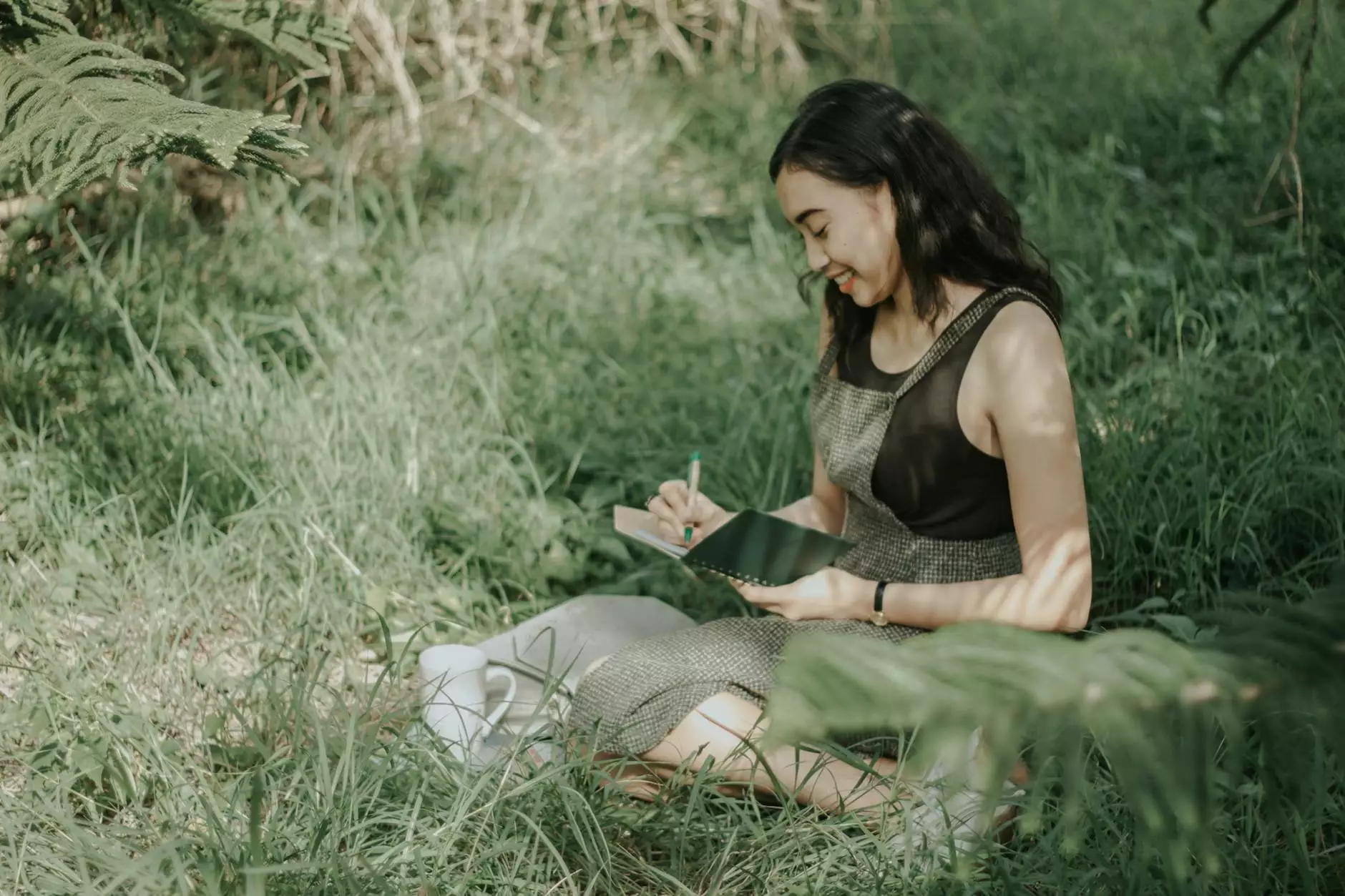
Pump cavitation is an essential topic for businesses involved in mechanical systems, particularly in areas such as auto repair, farm equipment repair, and structural engineering. This phenomenon can lead to severe operational challenges, including system failures, inefficiencies, and costly downtime. Understanding pump cavitation can significantly enhance your operational reliability and performance.
What is Pump Cavitation?
Pump cavitation occurs when the pressure in a pump falls below the liquid’s vapor pressure, leading to the formation of vapor bubbles within the pump. These bubbles subsequently collapse violently when they enter areas of higher pressure, causing shock waves that can damage the pump's impeller and other components. This process not only results in physical wear but can also lead to significant efficiency losses.
The Causes of Pump Cavitation
Numerous factors can contribute to pump cavitation. Below are some of the primary causes:
- Insufficient Inlet Pressure: If the inlet pressure of the pump is too low, it can cause cavitation. This might occur due to inadequate liquid levels in the supply tank.
- High Fluid Temperatures: As temperatures rise, the vapor pressure of the liquid increases, leading to a higher chance of cavitation at normal operating pressures.
- Pump Speed: Increasing the pump's speed can lower the pressure at the eye of the impeller, potentially leading to cavitation.
- Piping Issues: Restrictive piping or a sudden change in the direction of flow can create turbulence and turbulence-induced pressure drops, contributing to cavitation.
Identifying Pump Cavitation
Recognizing the signs of pump cavitation early can help mitigate its damaging effects. Here are some indicators:
- Unusual Noise: Cavitation often produces a distinct grinding or rattling noise within the pump due to the collapsing bubbles damaging the impeller.
- Power Fluctuations: A pump experiencing cavitation may require more energy to operate, indicating that something is amiss.
- Reduced Output: A drop in expected flow rates can signal cavitation, necessitating immediate investigation.
- Physical Inspection: Checking the pump impeller and housing for signs of pitting or erosion can confirm cases of cavitation.
The Effects of Pump Cavitation on Business Operations
For businesses, pump cavitation can have several detrimental effects:
- Increased Maintenance Costs: Frequent repairs due to cavitation can lead to higher long-term maintenance costs, impacting overall profitability.
- Reduced Equipment Lifespan: Continuous cavitation can significantly shorten the lifespan of pumps, necessitating early replacements.
- Downtime: In industries reliant on consistent operation, such as auto and farm equipment repair, downtime from cavitation-related failures can impede workflow and productivity.
- Efficiency Losses: Systems operating with cavitation can become less energy-efficient, causing higher operating costs and potentially impacting pricing strategies.
Preventing Pump Cavitation
Preventing pump cavitation involves a multi-faceted approach. Below are strategies that businesses can implement:
- Ensure Proper Installation: Adhering to guidelines during installation can help maintain appropriate inlet pressures.
- Monitor Pump Operation: Regular monitoring can help identify early signs of cavitation, allowing for timely interventions.
- Upgrade Equipment: Investing in high-quality pumps designed to resist cavitation can be a cost-effective long-term strategy.
- Adjust System Design: Reviewing and modifying piping design to minimize pressure drops can play a crucial role in preventing cavitation.
Troubleshooting Pump Cavitation
If you suspect that your business's operations are affected by pump cavitation, a systematic troubleshooting approach can help pinpoint the cause:
- Check Inlet Conditions: Ensure that the inlet pressure is adequate and that there are no blockages in supply lines.
- Inspect for Leaks: Look for potential leaks in the system, which can lead to pressure drops.
- Monitor Load Requirements: Evaluate the load on the pump and how it correlates with the current settings.
- Examine Pump Configuration: Verify that the pump is configured correctly for the application to avoid operational stresses that lead to cavitation.
The Role of Professionals in Managing Cavitation
For businesses engaged in auto repair, farm equipment repair, and structural engineering, collaborating with professionals experienced in pump cavitation management is invaluable. Such experts can conduct comprehensive system evaluations, recommend suitable equipment, and implement efficient maintenance routines.
Conclusion
Understanding and addressing pump cavitation is crucial for maintaining operational efficiency in any business dealing with fluid mechanics. By being proactive about the causes, effects, and prevention strategies, businesses can save considerable time and resources, ensuring smoother operations and healthier profit margins. Staying informed and working with experienced professionals can aid in mastering this challenge, contributing to long-term success.
About Michael Smith Engineers
At Michael Smith Engineers, located in the UK, we specialize in auto repair, farm equipment repair, and structural engineering. Our experienced team is dedicated to providing top-quality service, leveraging expertise to address challenges such as pump cavitation. Contact us today to learn about our comprehensive engineering services and solutions tailored for your business needs.